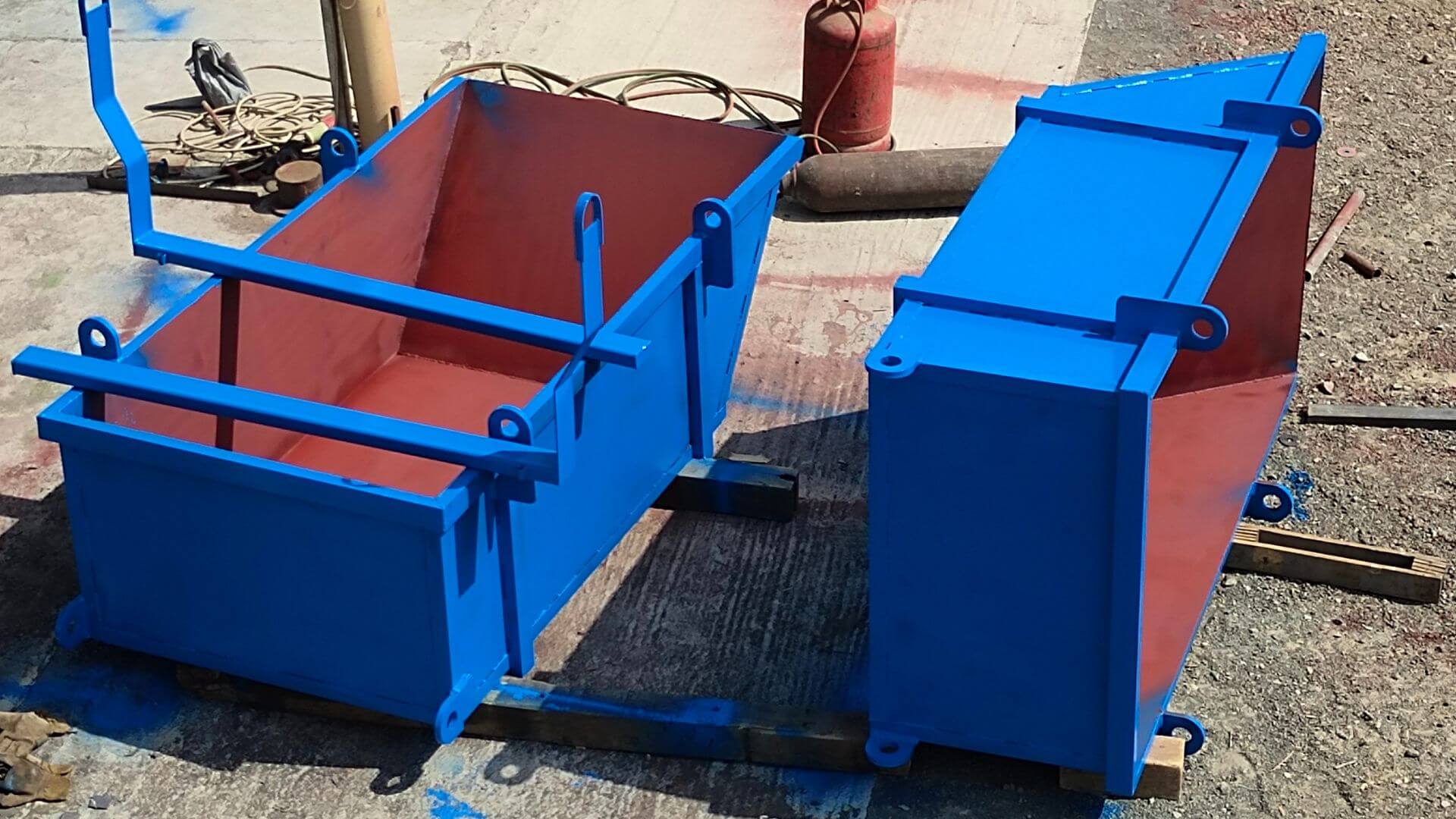
Waste Skip Manufacturing : Materials, Design, and Cost Factors
Waste skips are indispensable containers in construction, industrial, and commercial waste management. Manufacturing high-quality waste skips requires careful attention to materials, design, and cost considerations to meet durability, safety, and functionality demands. This blog explores the critical aspects of waste skip manufacturing and helps you understand what goes into producing these vital containers.
Materials Used in Waste Skip Manufacturing
The choice of materials significantly impacts the strength, durability, and lifespan of waste skips. Most skips are made from steel due to its excellent structural properties. Key materials include:
- Carbon Steel: The most commonly used material, carbon steel offers a good balance of strength, durability, and cost-effectiveness. It can withstand heavy loads and harsh environmental conditions.
- Galvanized Steel: Galvanized steel is coated with zinc to resist corrosion, especially important in humid or coastal areas like the UAE.
- Stainless Steel: Less common but used in specialized applications requiring high corrosion resistance and cleanliness, such as food or chemical waste skips.
- Reinforced Steel Sections: Certain parts of the skip, like the base or edges, may use reinforced steel for extra toughness.
Design Considerations in Waste Skip Manufacturing
Design plays a crucial role in ensuring skips are practical, safe, and easy to handle. Manufacturers consider various factors, including:
- Size and Capacity: Skips are designed in multiple sizes ranging from small 2 cubic yard bins to large 40 cubic yard containers to meet diverse customer needs.
- Shape: Typical skip shapes include rectangular, trapezoidal, and open-top bins for easy loading and unloading.
- Structural Integrity: Robust welding and reinforced corners enhance strength and prevent deformation under heavy loads.
- Loading and Unloading Features: Skips often include lifting lugs, hooks, or forklift pockets for easy handling by machinery.
- Drainage and Ventilation: Some designs incorporate drainage holes or ventilation slots to prevent water accumulation and reduce odors.
- Safety Features: Edges may be rolled or capped to reduce injury risk, and some skips have locking lids or covers for secure waste containment.
Manufacturing Process Overview
Waste skip manufacturing involves several steps:
- Material Preparation: Steel sheets and sections are cut to size using CNC machines or plasma cutters.
- Forming and Bending: Steel plates are bent into the required shapes for walls, base, and other parts.
- Welding: Skilled welders assemble the components, ensuring strong joints and smooth finishes.
- Surface Treatment: The skip is cleaned, sandblasted, and treated to remove rust and prepare for painting or galvanizing.
- Coating and Painting: Skips are coated with primer and painted using durable industrial paints to withstand outdoor exposure.
- Quality Inspection: Each skip undergoes rigorous inspection for weld quality, dimensional accuracy, and finish before delivery.
Cost Factors in Waste Skip Manufacturing
The final cost of a waste skip depends on multiple factors, including:
- Material Costs: Steel prices fluctuate based on global markets, directly impacting skip costs.
- Size and Capacity: Larger skips require more material and labor, increasing cost.
- Design Complexity: Customized features such as lids, special coatings, or reinforced sections add to manufacturing costs.
- Labor and Technology: Skilled labor and advanced machinery influence production efficiency and cost.
- Surface Treatment: Galvanizing or special paint coatings raise costs but extend skip lifespan.
- Transportation and Logistics: Delivery costs depend on skip size, weight, and delivery location.
Quality and Compliance Standards
Manufacturers must adhere to industry standards and regulations to ensure safety and reliability. This includes:
- Compliance with ISO standards for welding and steel quality.
- Adherence to local environmental regulations regarding coatings and emissions.
- Meeting safety requirements such as load ratings and lifting points.
- Following UAE-specific construction and industrial equipment standards.
Innovations in Waste Skip Manufacturing
Recent advancements in manufacturing technologies and materials have improved skip quality and efficiency. Innovations include:
- Use of automated welding robots for precision and consistency.
- Application of eco-friendly coatings reducing environmental impact.
- Modular skip designs allowing customization and easier repairs.
- Lightweight high-strength alloys to reduce overall weight without compromising durability.
Choosing a Reliable Waste Skip Manufacturer
When sourcing waste skips, consider manufacturers that offer:
- Proven track record with industrial and construction clients.
- Customization options tailored to your specific needs.
- Robust after-sales support including maintenance and repairs.
- Competitive pricing without compromising on quality.
- Compliance with local and international standards.
Conclusion
Waste skip manufacturing is a complex process balancing materials, design, cost, and quality to deliver durable, safe, and efficient waste containers. Understanding these factors helps businesses select the right skips for their operations, ensuring long-term performance and compliance with regulations.
Partnering with experienced manufacturers in the UAE ensures you receive skips designed to withstand the region's demanding environments, supporting your waste management goals effectively.
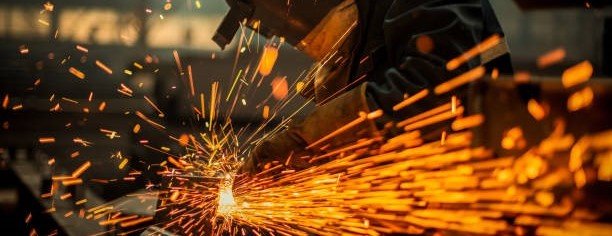